In 1978, when I was setting up to build my first boat, I needed to start accumulating tools. My shop was a temporary shed in the back yard of the house I grew up in, so my dad’s tools were available, but the only power tool he had was an electric drill. As a kid, I’d been able to get by with his tools making forts along the back fence, two bunkbeds for myself, and a darkroom in the garage, but they weren’t going to suffice for boatbuilding.The boat I started with was a dory skiff, and the limitations of Dad’s handsaws, hammers, and chisels came into sharp focus when I tried shaping its curved stem from a piece 2″-thick white oak. After I had traced the shape, I made dozens of short cross-cuts up to the line, whacked out the blocks in between with a chisel and a hammer, then finished up with a rasp and a file. It was painfully slow work, and I was pretty sure that if I ever finished the boat I’d never build another. One of these once-ubiquitous ads for Gilliom kits led me to building my first bandsaw.
Join The Conversation
We welcome your comments about this article. To include a photo with your remarks, click Choose File below the Comment box.
Of all the bandsaws I have known, I own the one that came to me, a Grob. You haven’t found a use for the powered saw or the multiple blades that I find a use for. But in the long run I couldn’t live without mine.
Great story, Chris, and excellent information about the different setups for the different bandsaws. I had just convinced myself that I didn’t need one to make a Greenland paddle….but you know the difference between need and want 🙂
Thank you for sharing the experience.
My first bandsaw was an 18″ Gilliom. Worked quite well, but was really a light-duty saw. I beefed it up, mainly the upright column plus added bracing for the top wheel support, which improved it. When I needed to cut out quite a few identical parts from a bronze water tank for a project, I put in a jack shaft and step pulleys, plus a metal-cutting blade, and it worked quite well in this mode. Eventually I sold that saw, and got a Grizzly 18″ (older style, with the cast-iron frame), and a Grizzly 14″ with the express purpose of converting it to a metal-cutting machine. I use it a lot, with 1/4″ variable pitch bi-metal blades that will cut bronze, mild steel, and even stainless. The blades last a long time. It will cut wood, too, but of course very slowly with its approx. 400 fpm. I don’t like it for aluminum as the fine teeth clog easily.
Just cut the aluminum on your woodworking bandsaw with a regular wood-cutting blade.
A table saw with a woodworking blade works fine too for straight cuts. Don’t raise the blade any higher than you need and wear 16 kinds of eye protection. Those aluminum chips are hard to get out of your eye with a magnet!!
Yes, I do cut aluminum on my table saw, but I hate the spray of chips that are thrown in my face. A full-face face shield is the minimum protection, and I also wear leather-welding gauntlets because those chips sting. I learned never to wear fleece while cutting aluminum, as the chips practically weld themselves into the fabric.
The blade on my big bandsaw has about 3 or 4 teeth per inch, making me leery about cutting anything thinner than 3/8″, or maybe 1/4″. Of course I could change blades, but find that an irksome chore.
My hypothesis about why it’s possible to cut stainless with the metal-cutting saw is that the blade has time to cool off as it leaves the metal to make its way around the wheels for another pass. I gave up long ago trying to cut stainless with a saber saw (aka jigsaw), as the heat destroys any blade within seconds.
Of course stainless cuts easily with a ferrous abrasive wheel on a 4.5″ angle grinder. Again, aluminum is somewhat problematic, as it clogs the disc. Even wheels intended for non-ferrous material tend to do this.
I’ve only owned one bandsaw, a 32″ Crescent that was an antique when I bought it about 40 years ago, when I started boat building. It has a 2-hp repulsion/induction motor, a replacement for the original of the same style. I have cut knees and breasthooks out of tree branches, resawn many thick chunks, cut frozen hams and turkeys (makes the saw run smooooth), and still use it all the time. Paid $150.00 for it.
I tried slicing bread with mine, but it created a lot of crumbs, and tended to leave metal chips on the bread. I’ve sometimes rued selling my manually powered miter saw, as I think it would excel as a bread slicer, but there would still be the crumbs.
Nice one, Chris!
A Greek boatbuilder and his bandsaw
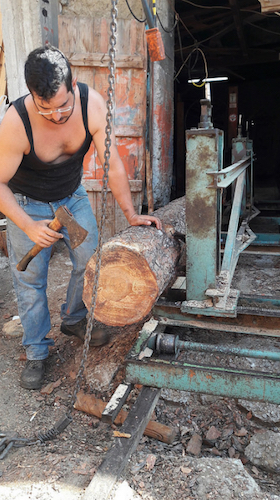
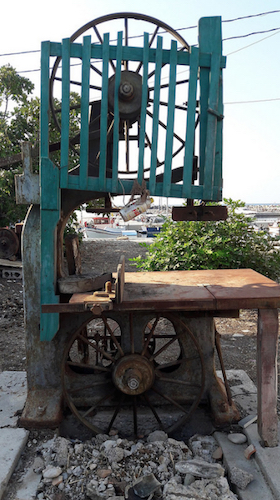
I’m a bandsaw geek! I’ve used a 20″ industrial bandsaw—I’ve owned three—a 10″ Delta, a nondescript 14″ saw and my grandpa’s crosscut metal saw. My question would be: can a horizontal/vertical bandsaw do both wood/and metal work?
In my opinion, a bandsaw with a standard wood cutting blade can cut aluminum. For harder metals (mild steel, stainless steel, and bronze or brass), I think the blade needs to be slowed down. With step pulleys on a jack shaft I got mine down to about 400 fpm. I use variable pitch bi-metal blades of only 1/4″ width. I prefer the narrow blade because it lets me cut curves. I get my blades made up by a local saw shop. I do sometimes make small cuts in wood, but the slow speed and fine teeth make that a slow process.
I think the smaller bandsaws (8″ up to 12″) flex the blade too much to be very satisfactory. The blades fatigue too quickly.
I have a 1946 two-speed Delta Milwaukee bandsaw, a 1946 Delta floor drill press, 1956 Delta shaper, an old Powermatic 16″ thickness planer and a 50-ish Boise Crane 10″ table saw and 6″ jointer combo. All old, used equipment but all quality pieces