Many years ago, while building small craft, I sought a solution for securing a hull under construction in different positions. It occurred to me that V-shaped sawhorses would maintain a V- or round-bottomed skiff in a secure working attitude whether upright, inverted, or in between. This would also work for a flat-bottomed hull, as long as the bottom was narrow near the ends, as a dory is.Consequently, I quickly and haphazardly conceived a simple design that could be implemented rapidly and cheaply, using standard 2×4 lumber. I build most of my sawhorses with legs cut to an acute angle on the flat on the upper ends, and cut to an obtuse angle on the bottoms, parallel to the shop floor. The upper angles are hard to cut through the width of a 2×4, so you rarely see sawhorses made this way. I do it because the horses are light, simple and strong, and use a minimum of material. I often gusset the ends with whatever scrap plywood is lying around the shop. The drop-center sawhorses were an improvement on my standard sawhorses which have survived at least 15 years of use outdoors. The old and the new horses have the same beveled connection between the legs and crosspieces.Reuel Parker
Join The Conversation
We welcome your comments about this article. To include a photo with your remarks, click Choose File below the Comment box.
I did the same by attaching a 1 ” piece of plywood to my sawhorse with a curve in it covered with carpet.
As usual, Reuel’s out-of-the-box, creative thinking solves a problem in a way that is logical, economical, not wasteful, and, most importantly, it WORKS!!
Reuel, you wouldn’t happen to have line drawings for this that I can be lazy and just download, do you?!
Wow, thanks so much for this post! The acute-angle-cutting jig described by the editor here simplified the labor of how the heck to cut a whole bunch of such shapes simply & safely. Very inspired here by The Sharpie Book; possibly ironic that the first “Reuel B. Parker design” I’ve built is a pair of sawhorses to hold a Sunfish 🙂
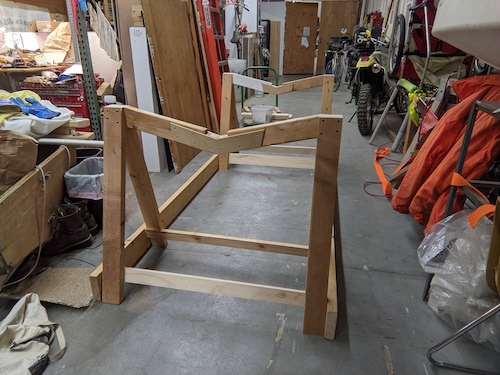
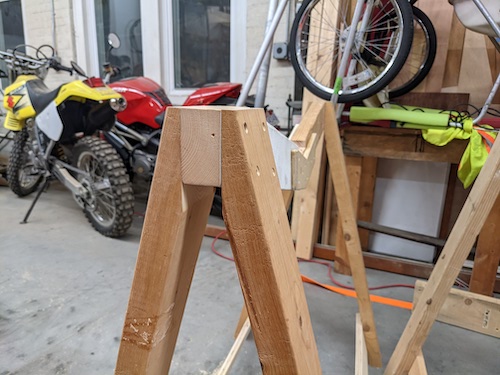
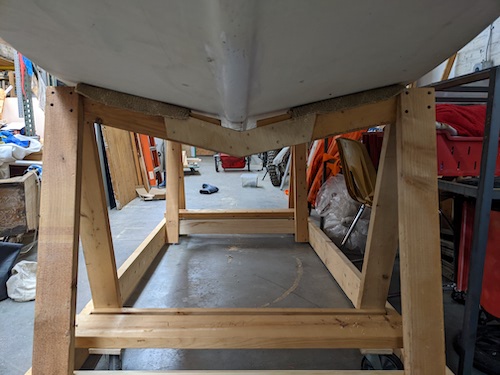
I used 15°/75° as the cut angles for the tops and bottoms of the legs, and just based the height dimension on the pieces of scrap 2x4s that I had available for the legs (aiming for just under 35″-36″, which worked out). The biggest change I made from Reuel’s design is to make the leg tops not quite as thin/pointy as his: the thickness of the tops of my legs is about 3/4″, to have something hearty to screw through into the crosspieces.
I built them into a rolling stand so I can work on this old 69-70 Sunfish and move it around by myself. With the rolling stand I’ll be able to take the boat outside to do my grinding/prep for the fiberglass work.